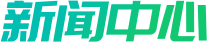
分享RayLink远程控制软件最新企业资讯以及行业前沿技术
制造业数字化转型:工业级远程控制方案选型指南
在“中国制造2025”战略与“双碳”目标的驱动下,制造业数字化转型已成为企业提升竞争力、实现高质量发展的核心路径。作为转型的关键支撑技术,工业级远程控制方案通过设备互联、数据驱动与智能运维,正在重塑生产管理模式。今天我们将围绕远程控制技术,结合行业实践与政策导向,为企业提供选型指南。
一、数字化转型背景下的远程控制需求
制造业的.需求源于三大核心场景:生产设备运维、跨地域协同设计、供应链实时调度。例如,某高端装备制造企业通过部署工业物联网平台,实现设备运行数据的实时采集与预测性维护,故障响应效率提升60%;而汽车产业链企业则依托私有化远程控制方案,在保障数据安全的前提下完成产线调试与工艺优化。
政策层面,《制造业企业数字化转型实施指南》明确提出:需加速工业互联网与人工智能技术融合,推动设备远程监控、智能排产等场景突破。这要求远程控制方案需满足高帧率画面传输、多协议兼容、工业级安全标准等特性,以适配复杂生产环境。
二、工业级远程控制方案选型要点
1. 明确需求与场景适配
企业需优先梳理自身痛点:
- 离散制造(如机械加工)侧重设备状态监控与工艺参数远程调整,需支持OPC-UA、Modbus等工业协议;
- 流程工业(如化工)则依赖实时数据驱动的远程决策,需强化APC(先进过程控制)与数字孪生集成能力;
- 多工厂集团型企业还需考虑跨地域协同与混合云部署需求。
2. 技术性能基准线
- 画面传输质量:4:4:4色域无损传输可确保设计图纸与精密检测画面的准确性,避免色差导致的工艺偏差;
- 低延迟与高稳定性:生产线控制指令需实现10ms级响应,防止因延迟引发的设备联动失调;
- 安全合规性:通过私有化部署、堡垒机隔离与端到端加密,满足《网络安全法》与行业数据管控要求。
3. 生态兼容与扩展性
优秀方案需兼容PLC、CNC机床、工业机器人等设备,并支持与MES、ERP系统无缝对接。例如,某企业通过集成远程控制与数字孪生平台,实现故障设备的“虚拟调试”,缩短了70%的停机时间。
三、RayLink远程控制在制造业的差异化优势
在众多解决方案中,RayLink远程控制软件凭借技术特性与场景适配能力脱颖而出:
1. 工业级视觉呈现能力
- 支持4:4:4色彩模式与120FPS超高清帧率,精准还原CAD图纸、3D模型与精密检测画面,满足汽车设计、半导体检测等场景的严苛需求;
- 多屏流式传输功能,可同步监控多条产线设备状态,提升管理效率。
2. 全链路低延迟交互
- 采用自研镭速传输协议,指令延迟低于10ms,适用于CNC加工参数远程调整、机器人轨迹修正等实时操控场景;
- 内嵌数位板压感识别技术,支持远程工艺设计协同,设计师可异地完成手绘稿与模型修正。
3. 安全与灵活部署
- 提供私有化部署方案,支持与企业AD域、SSO系统集成,满足汽车、航空航天等行业的数据合规要求;
- 设备分组管理与权限分级功能,可针对研发、生产、运维部门设置差异化访问策略。
4. 成本优化实践
- 通过预测性维护与远程故障诊断,某装备制造企业年运维成本降低35%;
- SaaS版支持按需订阅,中小型企业无需承担高额IT投入即可实现产线数字化。
结语
工业级远程控制不仅是技术工具,更是制造业构建柔性生产体系的核心引擎。RayLink以其卓越的画面精度、实时性与安全性,为企业提供了从设计到运维的全链路数字化赋能。在政策红利与技术迭代的双重驱动下,选型适配的远程控制方案将成为企业赢得数字化转型先机的关键筹码。
版权声明:本文内容由RayLink远程控制软件整理发布,转载时必须以链接形式注明原始出处及本声明。
相关阅读